Defining the Difference
A question we are often asked at RMP Products is whether there is a difference between bevelling and chamfering. The 2 terms are often used interchangeably, so is there a tangible difference between the processes, or are we splitting hairs? As is so often the case in these situations, it depends who you ask! In some less scrupulous industries it doesn’t make much of a difference, but in metalworking the 2 are clearly distinguishable.
Starting with the similarities, in both cases the processes involve removing material from the edge of a component to create a flat surface where there would previously have been a corner or burr. A simple illustration of the difference is seen in the diagram below:
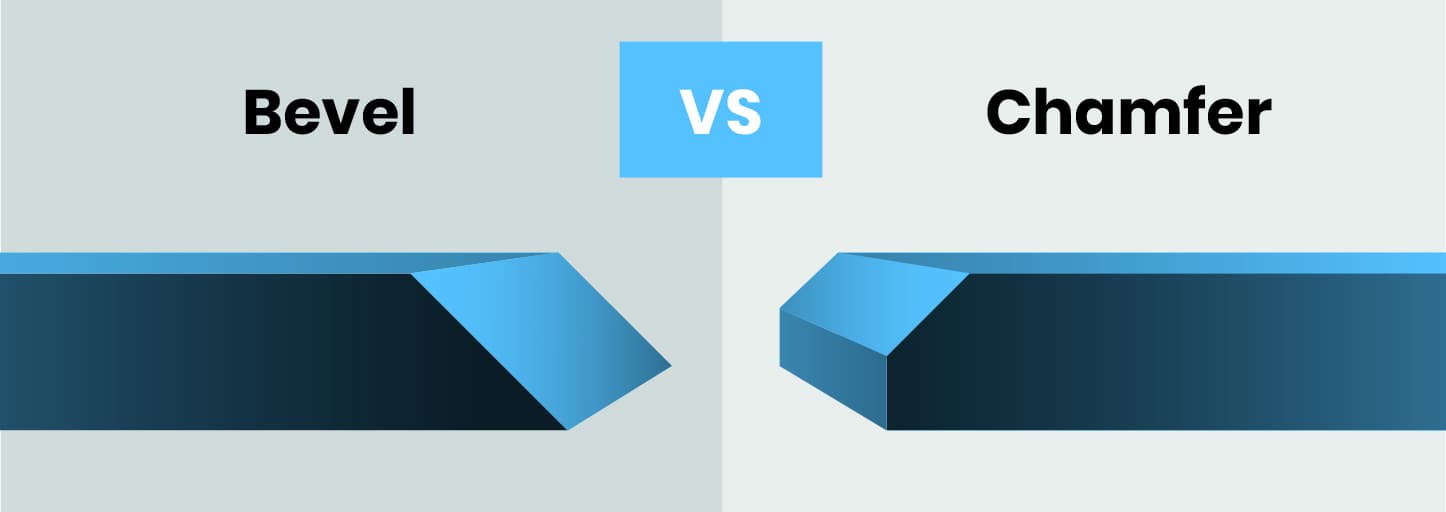
As you can see, the key difference between the 2 parts is that chamfering only removes enough material to create a new face on the component, rather than bevelling which removes enough material that a previously sraight edge is now at a desired angle.
The purpose of bevelling is to enable 2 pieces to join together at a desired angle or fit. 2 Beveled sheets would come together to form a V shape, rather than a right angle if they were not beveled. This allows fabricators and manufacturers to create a much wider variety of joins when welding metal.
The nature of the bevel itself also allows the welding process to work efficiently as the beveled faces of each component will be contacting each other on as much surface area as possible, allowing the molten metal created in the welding process to form a more solid and consistent bond.
Chamfering is usually done for decorative and practical purposes, for example on glass edge coffee tables or anywhere that sharp edges need to be removed chamfering is likely to be required. It’s common to see chamfering in woodworking as a decorative feature, particularly on architrave and on skirting board.
RMP Products can help with both of these processes, whether you require a single part to be processed in either of these ways, or whether bevelling and chamfering is just one step in a longer process, we can help with a variety of manufacturing requirements. To find out more you can contact us via phone on 0121 505 3066 or email at office@rmpproducts.co.uk